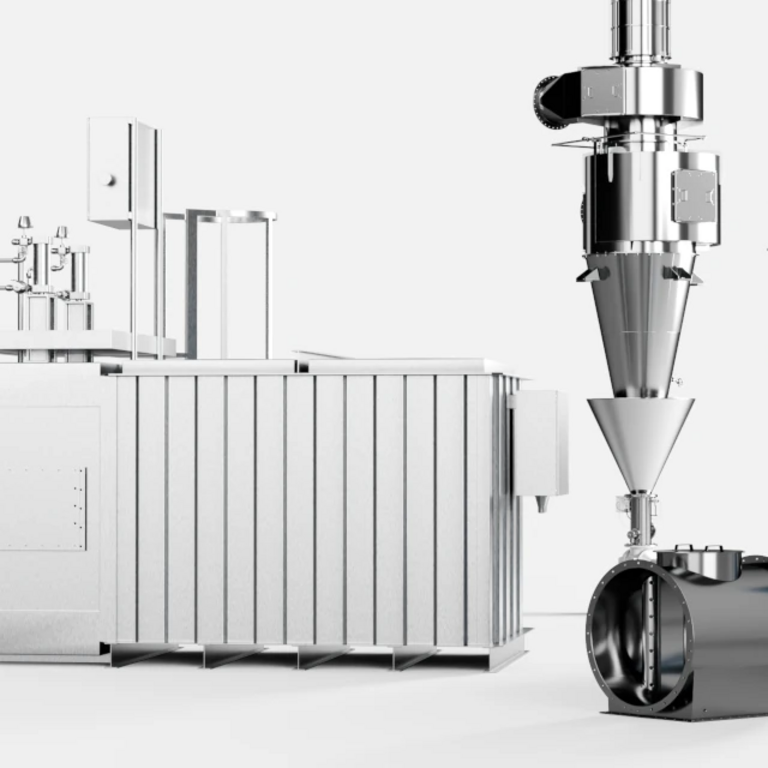
Environmental Technologies
Optimized Processes. Reduced Impact.
PROBAT’s innovative environmental technologies are designed to reduce energy consumption and optimize exhaust air purification – helping manufacturers achieve more sustainable operations. From advanced heat recovery systems to high-efficiency exhaust air treatment, our solutions support environmentally responsible production while maintaining high standards of process performance and compliance.